ProStore®-Module Goods Receipt
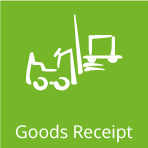
ProStore® provides the option of supporting various forms of the Goods Receipt with the module Inbound. In this case, a distinction is made between Goods Receipts by delivery, on the basis of forward data and advice or cross-docking. Of course, it is also possible to enter Goods Receipts without open orders. Frequently, mobile incoming workstations are used.
Delivery
As an upstream process for the collection of goods, ProStore® offers the possibility of recording a Goods Receipt / delivery before the actual collection. The purpose of the goods acceptance is to enable a fast unloading of the delivery vehicle and, at the same time, to identify the delivery LHM belonging to the delivery, so that a subsequent link to the order data delivered by the ERP solution can be produced during the subsequent incoming goods processing. A further advantage is that, in the event of bottlenecks on the goods entrance surface, a storage-accurate storage into other storage areas is possible.
For this purpose, a delivery number is generated in ProStore®, to which the delivered pallets / containers can be assigned. In this case, either a pallet label can be assigned or an already introduced NVE number or the supplier’s number can be taken. The marriage of the excellent pallets / containers with the newly created delivery and their storage space can be carried out using the MDE or ProStore® Desktop-Dialogue.
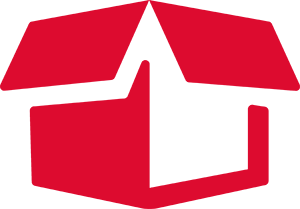
Cross-Docking
Cross-docking articles are marked accordingly in the WE notes and should already have an assignment to a customer order. They are fed into the consolidation or packaging process.
Supplier rating
Within the scope of the goods collection, valuation criteria can be recorded for defined suppliers. The criteria can be configured in the master data.
In the event of non-faulty deliveries, resulting extra costs can be recorded and transferred to the ERP solution.
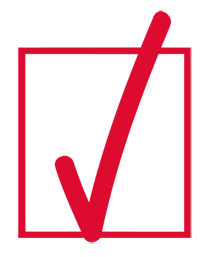
Goods collection
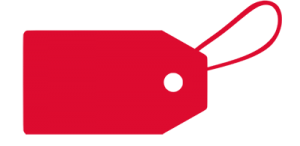
Collection of the deliveries and labeling of the pallets / containers for later exact identification based on open orders. Open orders are delivered by the ERP solution.
In this step, a dedicated assignment of different supplier batches on the pallet and container level is also possible.
Detection and collection of goods receipts by scanning (MDE) of the EAN-128 labels already present on pallets and processing of the associated DESADV data.
Generation of transport orders for the storage of the LHMs taking into account the respective storage strategy. These are processed via the ProStore®-integrated stacker guide system or, in the case of connected automatic storage systems, transferred to PLCs or MFR systems.
An unplanned goods receipt, that is, the collection of goods without an existing order, is in ProStore®
A goods receipt can be canceled completely or pallet-related.
Notification of received quantities to the ERP solution.
WE-Avise (from the ERP solution) on the pallet level can be processed. At defined I points, the pallets are checked against the notes. If they are used as aids, the pallet is automatically applied and the collection is carried out without manual intervention.